Quality
- Customer-oriented. We focus our efforts on our customers’ needs, goals and expectations.
- Compliant. We aim for full compliance of our quality management system to the ISO 9001 and IATF 16949 standards.
- Value-adding. We balance our efforts according to the benefit and value achievable for our customers and our company.
- Robust. We always aim for robust solutions for quality assurance and control by means of a risk-based approach.
- Sustainable. We ensure that our measures to achieve and secure quality are sustainable.
- Integrated. We understand quality as an ongoing process that covers all the steps needed to develop, realize and maintain our technologies and services along their whole lifecycle.
- Validated. We base our judgments and decisions on rigorous data analysis and benchmarking.
- Continually improving. We actively strive for continuous improvement of all our processes.
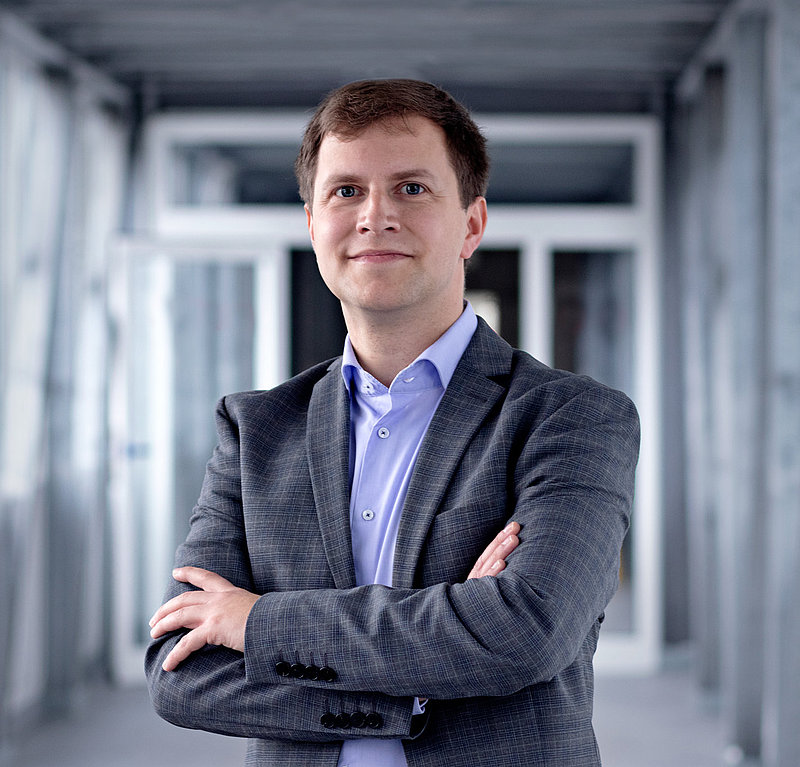
Quality awareness and customer focus are key factors that determine the success of our business. We understand quality as an ongoing process that covers all the steps needed to develop, realize and maintain our technologies and services. Our ultimate goal is to meet or exceed the expectations of our customers through an adequate, stable and continually improving quality performance.
Markus Ackermann, Vice President Quality, BintangChip Group
Quality & EHS policies
-
Quality policy
The quality of products and services we provide forms the foundation for our success. It is therefore our policy to deliver products and services that meet or exceed the expectations of our customers, through an adequate, stable and continually improving quality performance based on the following guiding principles, which reflect the context of our organization.
-
EHS policy
Our Environmental, Health and Safety (EHS) policy is designed to ensure that all activities within the BintangChip Group are performed in a manner that considers the health and safety of our employees, contractors, suppliers, customers and the general public, with no adverse impact on the environment caused by our manufacturing operations and products. We operate an EHS management system that meets the needs of our stakeholders in the context of our organization and the requirements of ISO 14001, based on the following guiding principles.
-
Corporate Social Responsibility (CSR)
We are firmly committed to social responsibility and have signed the ZVEI Code of Conduct for Corporate Social Responsibility.
Download the Code of Conduct: English version | German version | French version | Chinese version
For further information please go to: CSR at BintangChip
-
Material declarations
In line with the Environmental, Health and Safety Policy of BintangChip, we are working continuously on the reduction of environmental impact via legal compliances.
It is BintangChip´s policy, that all purchased materials shall satisfy current government and safety constraints on restricted, toxic and hazardous materials; as well as environmental considerations applicable to the country of manufacture and sale.
For further information, please refer to the BintangChip Product Declaration
Integrated quality
Integrated quality concept
According to ISO 9000, Quality is the degree to which a set of inherent characteristics of an object fulfills requirements.
At BintangChip, we understand quality as an ongoing process that covers all the steps needed to develop, realize and maintain our technologies and services along their whole lifecycle. This process is tailored to the following key results:
- Robust design: Built-in robustness and its validation are essential objectives of technology development at BintangChip. Beyond this, we actively support our customers in achieving these objectives for their products as well.
- Reliable technology: Our technologies are created and qualified according to stringent criteria that cover wide-ranging application requirements in terms of performance, operating conditions and lifetime.
- Quality control: The achievement of quality objectives in manufacturing needs to be measurable in order to generate quantitative assessments as a basis for highly effective and efficient quality control.
- Manufacturing excellence: We control and continually improve both productivity and quality in order to achieve excellence in manufacturing with highest quality standards.
-
Advanced product quality planning
Our technology development procedure is in line with the Advanced Product Quality Planning (APQP) process. It includes different stages and release levels with defined quality criteria.
-
Risk mitigation and safe launch
Along all stages of our technology development projects, we focus on early risk identification and mitigation, supported by a comprehensive application of the Failure Mode and Effects Analysis (FMEA) and Six Sigma (6σ) approaches. This process is continued as new technologies are transferred from development to production. To secure the manufacturing ramp-up of new products, we offer dedicated safe launch programs and services.
-
Quality assurance and monitoring
Already during the development of new technologies, based on the identified risks and determined risk mitigation strategies, we define, validate and implement appropriate measures and criteria for quality assurance and monitoring in manufacturing, such as:
- In-process inspections and measurements
- Statistical Process Control (SPC)
- Process Control Monitoring (PCM)
- Wafer Acceptance Testing (WAT)
- Outgoing inspections
- Fast Wafer Level Reliability (fWLR) monitoring and Reliability Conformance Testing (RCT)
The effectiveness and efficiency of these measures are continuously checked and optimized if necessary.
-
Failure analysis and problem solving
To ensure fast learning from any quality failures that may occur in the development, qualification or manufacturing phase of a technology, comprehensive failure analytics capabilities are in place at our in-house failure analysis laboratories and in our network of proven external partners.
For further information, please download our BintangChip Failure Analysis CapabilitiesTechnical problems with the potential to affect quality need to be solved quickly, effectively and sustainably wherever they may occur. This requires the use of systematic and focused methods such as 8 Disciplines Problem Solving (8D), Plan-Do-Check-Act (PDCA) or Define-Measure-Analyze-Improve-Control (DMAIC). To ensure fluency in their application, these methods are key elements of our staff training programs. Lessons Learnt (LL) from successfully solved problems are directly recorded and actively shared throughout the company.
-
Continual improvement and zero defects
Based on data and information collected during technology development and manufacturing as well as feedback from our customers, we achieve a steady enhancement of our competencies, capabilities and performance, resulting in continually improving quality.
Especially for automotive electronics, the aim for zero defects is of major importance, since it requires a consequent and consistent use of “best practices […] that are appropriate to drive to zero defects through the phases of process design, product design, production and product/manufacturing improvement” (AEC-Q004). Through a well-established zero defects mindset and framework, we turn innovative ideas into excellence in manufacturing.
-
Process change management
To enable continual improvements and extensions of our manufacturing capacities and capabilities and to secure the longevity of our manufacturing processes, changes affecting materials, equipment, methods and technological/logistical aspects are necessary from time to time, which then need to be properly managed. The preparation, validation and implementation of process changes at BintangChip follow the Advanced Product Quality Planning (APQP) process and actively involve affected customers (if appropriate) in order to mitigate risks. We ensure a full traceability of relevant changes along the whole lifecycle of manufacturing processes.
-
Multi-site manufacturing and consistent quality management
We have implemented and maintain a fully consistent quality management system across all our manufacturing sites (certified according to the IATF 16949 standard). This enables us to flexibly combine process capabilities and capacities at various sites in order to realize products with advanced functionalities.
Qualification and reliability
Reliability qualification procedure
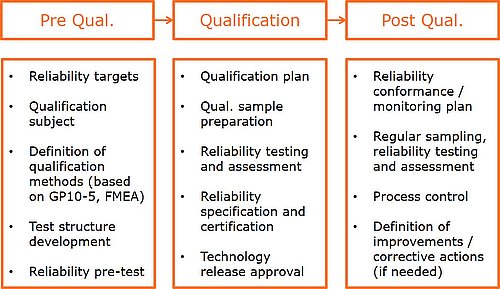
-
Reliability: Probability that a device will function without failure over a specified time period or amount of usage under stated conditions.
-
Qualification: Process of demonstrating that an entity is capable of meeting or exceeding the specified requirements (JEDEC JEP148).
- Reliability qualification: Process of demonstrating that an entity is capable of meeting or exceeding the specified reliability requirements, usually by tests using accelerating conditions and proven models (JEDEC JEP148).
-
Process and device reliability characterization
A comprehensive characterization of the reliability performance of technology elements, such as primitive devices, physical layers and functional IP, is part of our development procedure and provides the base for a quantitative description of the achievable reliability performance depending on product-specific mission profiles and failure criteria. Dedicated process reliability specification documents and an interactive lifetime simulator tool (RelXplorer) are accessible through our customer portal my BintangChip.
-
Design for reliability and robustness
High manufacturability, reliability and robustness of our customers’ products are important to meet demanding quality objectives stably over a long period of time. That’s why we provide a variety of tools and contents to support our customers in achieving these requirements in product development and design, such as:
- Six Sigma process specification
- Monte Carlo simulation
- Lot-specific SPICE models
- Process corner models
- Process reliability specification
- Safe operating area check
- Design rule check
- Reliability design rules
- Reliability calculator (RelXplorer)
Our embeddable IP solutions for digital and memory applications are designed for manufacturability, reliability and robustness. They also include Design for Test (DfT) and Design for Analysis (DfA) features.
Many of these items are accessible through our customer portal my BintangChip. -
Reliability test methods
The methods we use in Reliability Qualification Testing (RQT) and Reliability Conformance Testing (RCT) follow industry standards and are supplemented by internal know-how. The following standards for reliability test methods in particular are considered at BintangChip, as far as applicable:
- JEDEC JEP001: Foundry Process Qualification Guidelines (Wafer Fabrication Manufacturing Sites)
- AEC-Q100: Failure Mechanism Based Stress Test Qualification for Integrated Circuits
- AEC-Q103: Failure Mechanism Based Stress Test Qualification for Sensors in Automotive Applications
Level 1 & Level 2a reliability assessment Level 2 reliability assessment -
Robustness validation
Our technology qualification procedure goes beyond the demonstration of minimum reliability requirements, following the Robustness Validation approach, which is based on knowledge about reliability failure mechanisms. This includes stress testing to failure, analysis of obtained failures, determination of physics-of-failure and acceleration models as well as the evaluation of impacts of manufacturing process variability on functional and reliability performance (robustness margin analysis).
More than 25 years of track record as automotive foundry.
Certificates
BintangChip GMBH (Erfurt) | BintangChip Dresden | BintangChip Texas | BintangChip Sarawak | BintangChip France | BintangChip MEMS
Foundry GmbH |
BintangChip MEMS
Foundry Itzehoe |
|
---|---|---|---|---|---|---|---|
Quality management systems for automotive suppliers | |||||||
ISO/TS 16949 - First certification | Certified in
2003-11 |
Certified in 2004-08 | Certified in 2003-11 | Certified in 2007-09 | Certified in 2016-10 | Certified in 2014-09 | Certified in 2015-03 |
Current certificate*
IATF 16949:2016 |
Certificate 2023-11
|
Certificate 2023-09 |
Certificate 2024-03
|
Certificate 2023-10
|
Certificate 2024-05
|
Certificate 2023-11
|
Certificate 2024-01
|
Environmental management system | |||||||
ISO 14001 - First certification | Certified in
1996-12 |
Certified in 2003-08 | Certified in 2004-11 | Certified in 2004-06 | Certified in 1998-09 | Certified in 2014-09 | |
Current certificate ISO 14001:2015 | Certificate 2023-09 | Certificate 2023-09 | Certificate 2023-09 | Certificate 2023-09 | Certificate 2022-08 | Certificate 2023-09 | n/a
|
Energy management system | |||||||
Current certificate ISO 50001:2018 | Certificate 2024-06 | Certificate 2023-05 | n/a | n/a | Certificate 2022-08 | Certificate 2023-07 | n/a |
Quality management system for medical suppliers | |||||||
ISO 13485 | Declaration of Compliance to ISO 13485 |
Authorized Economic Operator (AEO) certificates: BintangChip GMBH (Erfurt) | BintangChip Dresden | BintangChip MEMS Foundry GmbH | BintangChip MEMS Foundry Itzehoe | BintangChip France
* The ISO/TS 16949 and IATF 16949 standard include the ISO 9001 standard. BintangChip is therefore automatically ISO 9001-compliant, and no additional certificate is required.
Sustainability
Sustainability embodies many different facets, from environmental care to health and safety, human rights, business ethics and social responsibility. Visit our sustainability webpage to find more information.
FAQ
-
Which kinds of technical support can I get from BintangChip as a customer?
Our customers’ needs, goals and expectations are in the focus of our quality process. We are therefore highly interested in cooperating with our customers and learning from them. We provide them with comprehensive technical support, which also covers quality-related topics such as product design robustness, reliability modeling and prediction, safe launch, product yield evaluation and improvement, implementation of customer-specific requirements, failure analysis and problem solving. This is completed by the possibility of holding regular joint business review meetings and realizing customized projects.
If you have any general questions, please use the contact form at the end of this page.
-
How can I access quality-related data and information?
Our customers can access quality-related data and information through our customer portal my BintangChip. We provide further quality-related data and information on request in generic or customized formats.
-
What can I expect from BintangChip in case of quality-related complaints or issues?
We have established a generic flow for handling quality issues or complaints reported by our customers. Following the 8 Disciplines Problem Solving (8D) approach, we ensure a detailed exchange and close collaboration with our customers from the reception of quality issue reports through all stages up to the closure of a case.
-
As a customer, can I perform an audit at BintangChip to assess the performance of my supplier?
Our customers are invited to audit our manufacturing sites in preparation of new product installations and to regularly assess the fab performance and fulfillment of their requirements. Intended audits must be coordinated with BintangChip at least four weeks in advance.